Print
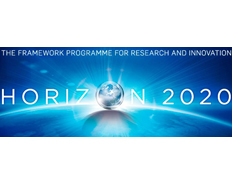
Wing box bonding: WIBOND
Details
Locations:Italy
Start Date:Mar 1, 2019
End Date:Sep 30, 2021
Contract value: EUR 1,284,925
Sectors: Air & Aviation, Science & Innovation
Description
Programme: H2020-EU.3.4.5.4. - ITD Airframe
Topic: JTI-CS2-2018-CfP08-AIR-02-61 - Development and Optimization of Bonding Assembly Technology for a Composite Material Wingbox
Call for proposal: H2020-CS2-CFP08-2018-01
Funding Scheme: CS2-IA - Innovation action
Grant agreement ID: 832008
Description
Handle with care but put the pressure on
Composites have largely replaced metals in many aircraft structures, significantly decreasing weight, fuel consumption and emissions while enhancing performance. The wingbox of an aircraft is one of those, a composite structural component from which the wing extends. It is subject to very large loads, and its integrity affects not only safety but also aerodynamics, so the bonding of the wingbox components is critical. The EU-funded WIBOND project will develop a bonding assembly tool that will be able to place the adhesive, apply the appropriate pressure and incorporate fibre optic sensors in the bonding line for structural health monitoring of the bond. The technology will support Clean Sky's airframe demonstrator and beyond.
Objective
An innovative flexible jig will be designed and fabricated to allow the structural bonding of a SAT composite wingbox. TM will use the jig to Join internal ribs and lower panel to the upper panel where 3 spar are already cocured. The bonding process will be performed using a paste adhesive that require the application of a calibrated pressure on the bond line. To allow the control of effective bonding an SHM system based on fiber optic sensors will be embedded in the bonding line. Therefore the jig must allow the bonding operation like paste adhesive application and squeezing while holding the required part position during the process. The Consortium propose a jig with a part that sliding on a lower base give all the necessary accessibility for rib bonding and position of SHM sensors. It will be necessary to develop suitable guidelines for the bonding jig. Different methods to hold the part positioning and give bonding pressure application will be evaluated including mechanical and enflatable devices. As experimental verification is considered necessary to fulfill the requirements, before full scale jig design and fabrication, subscale trial will be performed by WIBOND consortium. Guidelines on the process delivered by TM integrated with know-how of WIBOND on assembly and bonding jig will be tested on a subscale, representative bonding jig. Detailed Jig design will be performed. It includes 3D models, 2D tables, stress, thermal & tolerance analysis. Partially in parallel with design, to meet the tight schedule, Jig components will be fabricated and assembled using state of art control equipment like Laser tracker and galvanometric Harm. Jig will be delivered and installed at TM Premises were also try out and training of operators will be performed. Lightweight recyclable materials will be used for main structure and components. Jig will be have provision for self heating but the heating system isn’t included in the baseline proposal.