Print
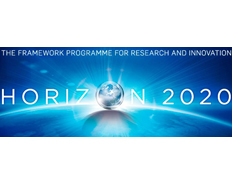
INdustrial LEvitation Technology - INLET
Details
Locations:Finland
Start Date:Sep 1, 2019
End Date:Jan 31, 2020
Contract value: EUR 71,429
Sectors: Electrical Engineering, Science & Innovation
Description
Programme(s):
H2020-EU.3. - PRIORITY 'Societal challenges
H2020-EU.2.3. - INDUSTRIAL LEADERSHIP - Innovation In SMEs
H2020-EU.2.1. - INDUSTRIAL LEADERSHIP - Leadership in enabling and industrial technologies
Topic(s): EIC-SMEInst-2018-2020 - SME instrument
Call for proposal: H2020-SMEInst-2018-2020-1
Funding Scheme: SME-1 - SME instrument phase 1
Grant agreement ID: 876049
Project description
Levitating bearings make industry more sustainable
About 40 % of the world’s electricity is consumed by rotating machines, but all these machines rely on physical ball bearings and lubrication. This means inefficient energy usage, high levels of wear and tear (lifetime costs), and environmental contaminants as waste products. The INLET project has developed a frictionless bearing system called SpinDrive that uses magnetic levitation to increase performance, lifespan and environmental friendliness of industrial machinery. SpinDrive lowers lifecycle costs of manufacturing machinery by 35 %, halves energy loss (thus reducing carbon emissions), and promises 20 years of maintenance-free operation, saving on average EUR 500 000 over the product lifetime. INLET machines are also completely oil-free, and incorporate cutting edge sensor and controller technology.
Objective
About 40% of the electricity worldwide is consumed by rotating electrical machines. However most of the electrical machines are not working at the optimum point from a process efficiency perspective. The electricity demand is growing and simultaneously greenhouse gas emissions must be significantly cut every year according to global agreements and regional terms of legislation. Cost-effective high efficiency motor development is highly required. SpinDrive provides highly efficient turn-key drivetrains (INLET), supported by frictionless magnetic bearings, for Original Equipment Manufacturers. INLET increases OEMs solutions’ system efficiency by at least 10%, reduce material consumption and simplify an equipment installation process. INLET lowers the customer’s lifecycle costs by 35%. INLET reduces energy losses in the machine by half. For a 500-kW unit, this solution mitigates 200 tons of CO2 emissions annually and enables 4-year payback time. INLET enables 20 years of maintenance-free operations and saves on average more than 500 000 EUR on the maintenance costs during the product lifetime. INLET is completely oil-free, which allows OEM customers to enter rapidly growing markets and ensure an alignment with a contaminant-free environmental strategy. Compared with the other magnetic bearing providers, SpinDrive can design the entire drivetrain and make it more cost efficient. Our sensor and controller technology enable 70% lower cost level and competitive pricing of delivered products. SpinDrive is a spin-off of Lappeenranta University of Technology, Finland, founded in 2015. Our INLET innovation builds upon the high-speed technology research at the university during the past 35 years. INLET has already reached TRL7 and a solid SMEI-1 feasibility study will guide our future growth as it will be used to acquire deep understanding of the market, competitors, customer segments, end-users and stakeholders and enable us to reach TRL 9 through the SMEI-2 by 2021.